As one of the China’s leading cut resistant gloves manufacturers since 2009, Ningbo Toprise Security Products Co., Ltd would like to share how to choose the right cut resistant gloves for all our dear customers. The blog is trying to introduce some common materials for producing cut resistant gloves and the two standards (ANSI and EN388) for the cut resistant gloves.
Importance of Cut Resistant Gloves
Cut-resistant gloves are very important for work places with sharp objects, knives, glass and metal. The gloves are mainly to reduce the hand injuries, which meanwhile would increase productivity and decrease permanent disability.
Materials for Cut-Resistant Gloves
Mainly there are 4 types of materials for producing the cut resistant gloves, in which Kevlar and Dyneema are two of the most world-famous brands. Below is a brief view of the 4 materials.
Kevlar Gloves
Kevlar is a kind of Aramid fiber, widely used in producing body armor, protective clothing, and industrial heat-resistant items. The gloves out of the aramid fiber are very strong, especially in tensile strength, but not so strong as Dyneema per weight. Kevlar is usually heavier and less flexible than Dyneema. So as far as comfort is concerned, Kevlar is not so good as Dyneema. But Kevlar gloves are quite heat resistant, making it very suitable for using in welding, metalworking, and firefighting. Also keep in mind that Kevlar gloves would degrade over time under UV light.
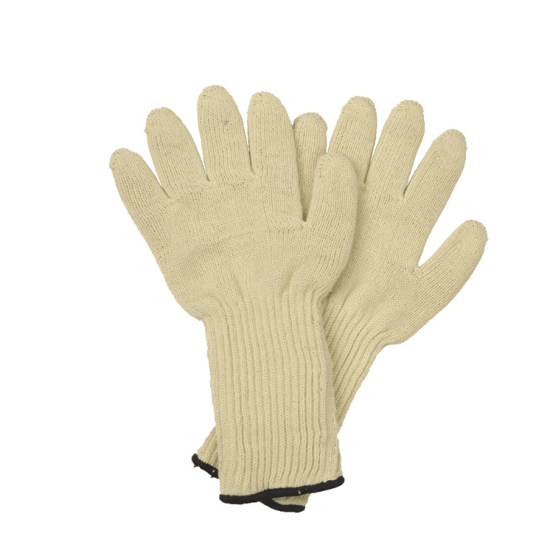
Dyneema Gloves
Dyneema is actually a kind of branded HPPE material. As a material claimed to be 15 times stronger than steel by weight, Dyneema gloves are extremely strong, lightweight and flexible. Workers often wear the cut resistant Dyneema gloves for food processing, glass handling, metal fabrication, and automotive assembly. Unlike Kevlar, Dynnema gloves are not heat resistant. But they offer excellent chemical resistance and are often coated with nitrile or latex for chemical-resistance enhancement. Below is a table to show the types of chemicals Dyneema can resist:
Chemical Category | Examples | Resistance Level |
Alkalis | Sodium hydroxide (lye) | Good |
Potassium hydroxide | Good | |
Acids | Dilute sulfuric acid | Fair |
Hydrochloric acid (low concentration) | Fair | |
Solvents | Ethanol | Good |
Acetone (limited) | Fair | |
Methanol | Good | |
Oils and Greases | Mineral oils | Good |
Vegetable oils | Good | |
Hydrocarbons | Gasoline | Good |
Diesel fuel | Good | |
Limitations | Strong acids (e.g., concentrated sulfuric acid) | Poor |
Aromatic hydrocarbons (e.g., benzene, toluene) | Poor | |
Halogenated solvents (e.g., chloroform) | Poor |

HPPE Cut Resistant Gloves
The full name for HPPE is high-performance polyethylen. Although they cannot work as well as the two branded cut-resistant materials, HPPE gloves are much more affordable. Similar to Dyneema gloves, workers often use the cut-resistant and chemical-resistant HPPE gloves in construction, manufacturing, warehousing, food processing and automotive industries.
Steel Mesh Gloves
We often take the steel mesh gloves with interlocked stainless steel rings or wire as the ones of highest cut resistant levels under standards like EN 388. Resistant to tear and wear, and easy to clean and sterilize, the mesh gloves are widely used in food processing, butchery and medical environments.

Cut-Resistance Levels & Applications
EN 388 Standards (EU market) & ANSI/ISEA 105 Standards (US market) are the two different standards for cut-resistance levels testing.
ANSI/ISEA 105 Cut Levels & Applications
The pic below is a brief short review on the application and the relevant cut levels under ANSI.
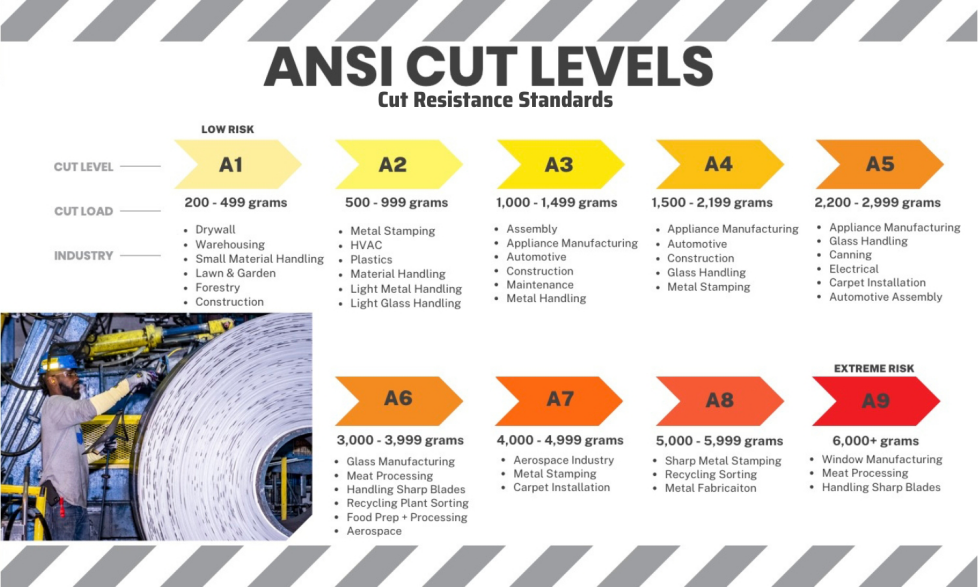
How to Read an EN 388 Label
See an example EN label on the back of gloves as below:
Hazard | Resistance Rating |
Abrasion Resistance | Level 4 |
Cut Resistance | N/A |
Tear Resistance | Level 4 |
Puncture Resistance | Level 2 |
ISO Cut Resistance | Level E |
Impact Resistance | Pass |
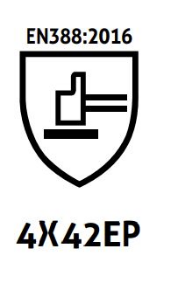
Other Details on EN388 Gloves
Further details on the Abrasion Resistance, Cut Resistance, Tear Resistance, Puncture Resistance & ISO Cut Resistance are as charts below:
ALL ABOUT ABRASION
Resistance Level | Abrasion Cycles |
Level 1 | Minimum of 100 cycles |
Level 2 | Minimum of 500 cycles |
Level 3 | Minimum of 2000 cycles |
Level 4 | Minimum of 8000 cycles |
ALL ABOUT CUT RESISTANCE
Cut Resistance Rating | Number of Cuts Withstood |
Level 1 | 1.2 cuts |
Level 2 | 2.5 cuts |
Level 3 | 5 cuts |
Level 4 | 10 cuts |
Level 5 | 20 cuts |
Here’s a table summarizing the cut resistance levels (1 to 5) according to the EN 388 standard, along with their applications:
Cut Resistance Level | Level (1-5) | Performance Rating (N) | Typical Applications |
Level 1 | 1 | 1.2 N or less | Light handling, general maintenance, packaging |
Level 2 | 2 | 1.3 – 3.4 N | Light assembly, food preparation, warehousing |
Level 3 | 3 | 3.5 – 5.4 N | Construction, automotive, light manufacturing |
Level 4 | 4 | 5.5 – 9.9 N | Glass handling, metal stamping, heavy assembly |
Level 5 | 5 | 10.0 N and above | High-risk environments, metal fabrication, heavy construction |
ALL ABOUT TEAR RESISTANCE
Tear Resistance | Tear Force (Newtons) |
Level 1 | 10N |
Level 2 | 25N |
Level 3 | 50N |
Level 4 | 75N |
ALL ABOUT PUNCTURE RESISTANCE
Resistance Level | Puncture Forces (Newtons) |
Level 1 | 20N |
Level 2 | 60N |
Level 3 | 100N |
Level 4 | 150N |
ALL ABOUT ISO CUT RESISTANCE
Here’s a table summarizing cut resistance levels and their applications according to the EN 388 standard:
Cut Resistance Level | Level (A-F) | Performance Rating | Typical Applications |
Level A | A | 1-2.5 N | Light handling tasks, packaging, assembly |
Level B | B | 2.6-5.0 N | General handling, warehousing, food prep |
Level C | C | 5.1-10.0 N | Light manufacturing, automotive assembly |
Level D | D | 10.1-15.0 N | Construction, metal stamping, glass handling |
Level E | E | 15.1-22.0 N | Glass handling, heavy-duty assembly |
Level F | F | 22.1 N and above | High-risk applications, metal fabrication, heavy construction |
Equivalents between ANSI and EN388 Cut Levels
Below is a pic showing how the ANSI corresponds to EN388 related to cut resistant gloves.

Conclusion
In a nutshell, make sure the cut resistant level is correct first or turn to us for more professional advice. Whether it is EN388 or ANSI/ISEA 105 standard, both of them are a good guide to help you get the right cut resistant gloves.